|  | Fairyglass Is... |  | 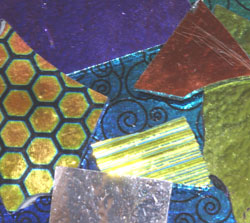 | The Magic Material Dichroic glass is a complex material. The base glass is usually handmade, rolled while molten. The dichroic layer is produced by depositing metal oxides in extremely thin layers via a vacuum process- some layers are less than one millionth of a centimetre thick. These metal oxides filter visible light, reflecting some frequencies and transmitting the remainder. Depending on the angle of view, the visible frequencies change and so the glass can appear to change colour as it moves.
Originally developed by NASA for use in the space programme, craftworkers soon realised the potential of dichroic glass and the first dichroic glass art products became available during the 1990s. When the glass manufacturers realised there was a new, secondary market for the dichroic coating, they began to produce slightly less technical versions for the art glass industry. It's this glass we use today- there are hundreds of varieties of colour and pattern to choose from.
Below you can read a little bit about how we produce our dichroic jewellery. Every glass artist uses similar basic techniques- the difference is how each artist interprets the glass, and combines both raw materials and skills to produce the finished article. Once you've read the details, take a few moments to visit our jewellery shop where we offer a wide range incorporating many different techniques.
|
How's It Made? Dichroic glass jewellery is no different from other fused glass in that it's made by heating layers of glass in a kiln until the glass melts and fuses together. Sections of dichroic glass are cut, mostly by hand, from larger sheets, and laid up in stacks (see left). These stacks can be anything from two to twenty-five or more layers, depending on the complexity of the piece. We typically use four to six layers into our pendants, depending on the type.
The final colour of the jewellery piece is dependent on the way that the layers are laid, how they interact with those above and below them, and how they move in the kiln when molten. Some pieces are made using opaque colours as backing glass which gives a more striking colour. Other items are made using translucent glass with a dichroic coating as backing which gives a more ethereal colour and these pieces are able to pick up colours from surrounding clothes etc, and change tone and hue. Most pieces available on the market are "capped" with a top layer of clear glass. This is the traditional finish, which results in a pebble of glass with rounded edges. We also use an uncapped process, which leaves the dichroic coating uncovered. The advantage of this is that the colours are a lot more vivid, but the pendant does lose the rounded look.
| 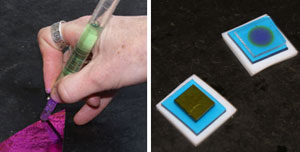 |
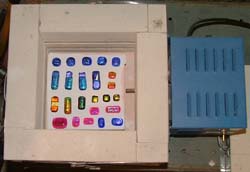 | The Kiln. Each piece is made by hand and unique - even two with the same glass colours and layouts will emerge from the kiln differently. As the glass melts in the kiln (up to around 800 degrees centigrade) the layers merge and colours flow, as the glass is in a liquid state. The severe heat in the kiln can alter the original colour of the glass, so the skill of the glassworker is to know how each type of glass reacts both to heat, and to other colours blending with it. The glass is then cooled using a complex thermostatic program, which holds the cooling glass at certain temperatures to allow the molecules to align properly, which strengthens the finished product- this is called Annealing.
The kiln is probably the most expensive tool in the glassworker's workshop, and there are many different types. Most glass enthusiasts and small scale studios opt for electric kilns with a digital programmer, which allow extremely precise control of the temperature. This is crucial, as a 10 degree variation can make the difference between a perfect piece and a lump of scrap! Every kiln is different - rather like an oven, it takes time to get to know the variations of temperature, hot spots, etc.
Once the glass has cooled- the kiln process can take up to eight hours- the piece can be worked to produce the final item. Some pendants, such as our Pendants With Silver Bails, are ready as they are, with the exception of adding a bail for the chain to pass through. |
Glass Shaping and Processing. Other pieces need to have further work before they are ready for presentation. Our Mermaid's Jewels are cut from larger pieces of glass using a specialist water-fed diamond coated saw, which is capable of cutting glass without breaking it. These pieces are then put back in the kiln, at a lower temperature, to "fire polish" the edges and make the piece shiny all over.
Offcuts of glass are not wasted- almost all pieces can be reused, even the smallest fragment. Take a look at any glass workshop and you'll see pots of shards- these are either combined into new jewellery items or melted down and used for backing glass. There is a risk here for the glassworker however- different glass makes expand and contract at different rates, and so they can't be mixed in a single piece as the variations are enough to crack a finished pendant. It's important if a workshop uses more than one brand to keep the shards seperate- there's nothing more heartbreaking than working on a piece for a long time, only to open the kiln and find it broken! | 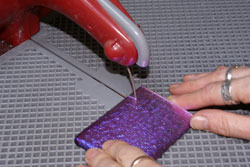 |
 | Other Shapes. Other techniques used to produce the dichroic glass we sell include "slumping" which is a gradual heating of glass over a mould, so that it softens and forms the shape of the mould, as used in our Slumped Earrings. We occasionally use torchwork to make our jewellery, which used a blowtorch instead of the kiln to melt the glass, which is then shaped by hand. We use a variety of specialist glass tools and equipment to achieve specific shapes- some can be cut using a machine, while others require manual cutting and shaping.
Pendants are sometimes cold worked by drilling or cutting with a fine glass cutter to shape them. Some pieces are re-fired once or even twice- a firing is usually done overnight due to the time it takes. This means that, taking kiln time into account, a single pendant may take up to 24 hours to produce. Even without kiln time, there is often an hour or more in production time, plus the raw material cost- many of the dichroic pendants and other dichroic jewellery you see on the market is severely underpriced!
A growing number of glass artists are turning to kiln casting to form complex pieces- the glass is melted in a mould in the kiln, and then sets to the shape of the mould. Shapes that would otherwise take hours of cutting are possible in a much quicker time, although often the moulds take hours to form in the first place.
|
Care & Attention. Dichroic glass jewellery needs no more care than any other type of glass or jemstone jewellery. You should take care not to let the piece come into contact with abrasives as scratching the glass may inhibit the colour-changing qualities. Otherwise the glass is as robust as any other glass item and you can wear it with confidence!
Some of the pieces we supply are set in metal wire or use metal clasps. Where possible we specify Sterling Silver for these in case of allergy and we try to note on the product description whether Sterling Silver has been used. If you are in any doubt please contact us- we're here to help.
To see our range of jewellery, click here
| 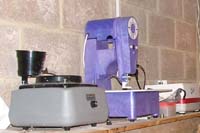 |
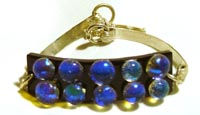 | We, the Fairyglassers.... We began Fairyglass because we love dichroic glass. The range of possible colours and designs is limited only by one's imagination. We began as hobbyists, and although it's now a full time business, we're still learning, and if you visit this site from time to time you'll see new products appearing as we experiment and as we become more confident! However it's more than just the making... we've found that you like wearing it also! For us, selling something beautiful at a fair price and giving someone pleasure by wearing it is a core element of the business. We aim to offer a range of jewellery that's value for money, with friendly and efficient service at all times, and to try to give a little more than our competitors. We don't want to be big- we feel it's better to make a living doing things in a way that we'd like to experience when we shop.
We love to hear feedback on our business- good or bad. You can see that we have a testimonials page where we publish your comments. If you've a criticism, please let us know- we can't improve without feedback. |
| Spot the Fairyglass! We're regularly at events throughout the South and Midlands. If you're an event organiser, please click here to contact us, to see if we can come to your event. If you're a customer, or potential customer, come and see us- we'd love to meet you and have a chat. If you'd like to know where we're planning to be in the near future, please click here to contact us, | ![Spot the Fairyglass!]() |
|
 |
| Fused dichroic glass jewellery by Fairyglass | Jewellery Shop | Terms And Conditions | Site MapAll text and images copyright Fairyglass 2008. Fairyglass is a registered trade mark. |